When to Use Hydraulic Fluid Additives
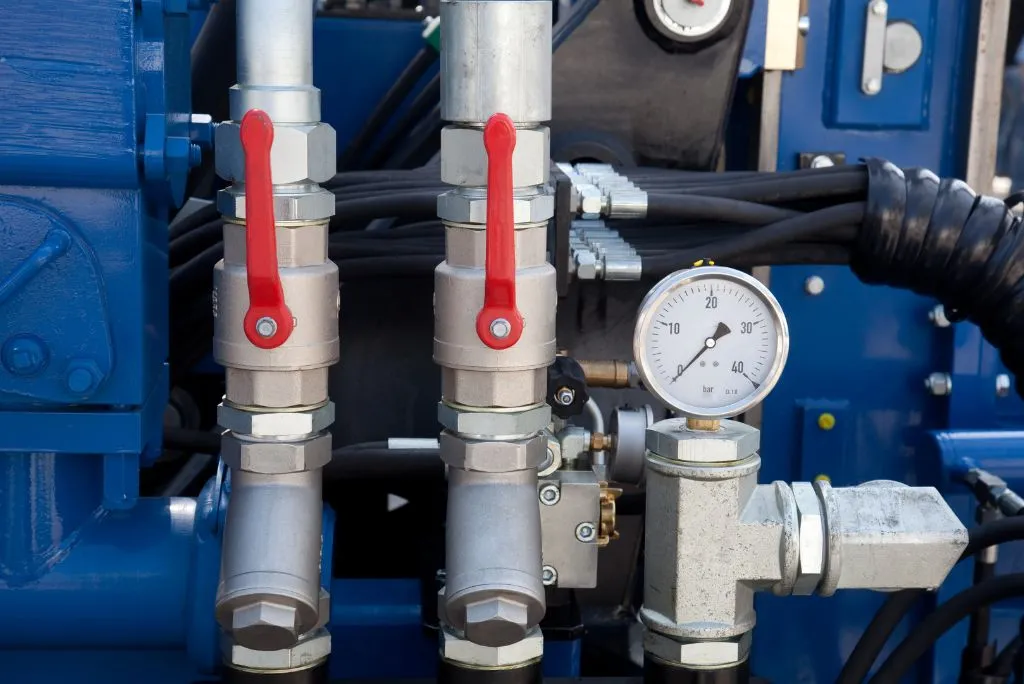
The fluid in a hydraulic system is the primary consideration. However, not every type of hydraulic oil works in every machine. In addition, it is not easy to locate the optimal fluid for any given system.
Hydraulic fluid additives find their most common application. The base oil can be modified to have the desired characteristics by adding the appropriate additives. Oil additives can boost desirable properties, reduce undesirable ones, or even add new ones to the base oil.
Components of Hydraulic Fluids and Their Meanings
Additives are used in concentrations ranging from 1% to 35% to achieve the desired oil properties. If the system is designed with the desired oil property, it can use additives or additive packages, additive mixtures, or add packs.
Among the many benefits, additives can bring to fluid is emulsification, increased reserve alkalinity, higher extreme pressure resistance, pesticide activity against microorganisms, boundary lubricity, antimisting, temperature stability, filtration improvement, and rust prevention.
Understanding Hydraulic Fluid Additives
According to their intended purposes, hydraulic oil additives can be separated into surface-active and active additives. Additive systems can also be used to categorize hydraulic oils.
1. Inhibitors of Wear
Zinc-based antiwear hydraulic fluids, also known as ZDDP hydraulic fluids, are the most widely used type of hydraulic fluid.
ZDDPs are commonly used in crankcase lubricants, driveline lubricants, and a wide variety of industrial lubricants because they are highly cost-effective antiwear agents.
2. Demulsifiers
Water in the hydraulic fluid can be quickly drained thanks to demulsifiers, which help separate the two. One strategy for preventing hardware from rusting and corrosion and decreasing system sludge is to remove any available water from the system.
Demulsifiers play a crucial role in the fluid, but they are usually present at deficient treatment levels, often below 100 mg/kg. Demulsifiers are typically mini formulations containing multiple components like treaters, water droppers, and clarifiers.
3. Antioxidants
Sludge and varnish can be produced when oxygen reacts with a base oil and additive components, producing alcohol, peroxide, aldehyde, ketone, and carboxylic acid species. The temperature boost accelerates these reactions.
Carboxylic acids are an oxidative degradation product that can promote rust or accelerate the corrosion of yellow metals. The harmful effects of oxidation can be avoided or mitigated with the help of antioxidant components.
4. Substances that Prevent Copper and Yellow Metals from Oxidizing and Rusting
Many electrochemical and chemical corrosion forms can affect the metallurgy in hydraulic systems.
Hardware made from copper alloys can be shielded from corrosion with copper and yellow metal passivation, while hardware fabricated from ferrous metals can be kept from rusting with rust inhibitors. Triazoles, a class of nitrogen-containing chemicals, are commonly used for passivation because of their high solubility in oil and other lipids.
5. Antifoams
Too much foaming, or air bubbles at the fluid’s surface, can cause cavitation damage, shorter fluid life due to oxidation, poor equipment lubrication, increased fluid compressibility, noise, and air entrainment.
Formulators use antifoam agents to avoid these issues. Antifoams destabilize air-fluid interfaces to collapse air bubbles.