What to Do With Hydraulic Fluid Leaks
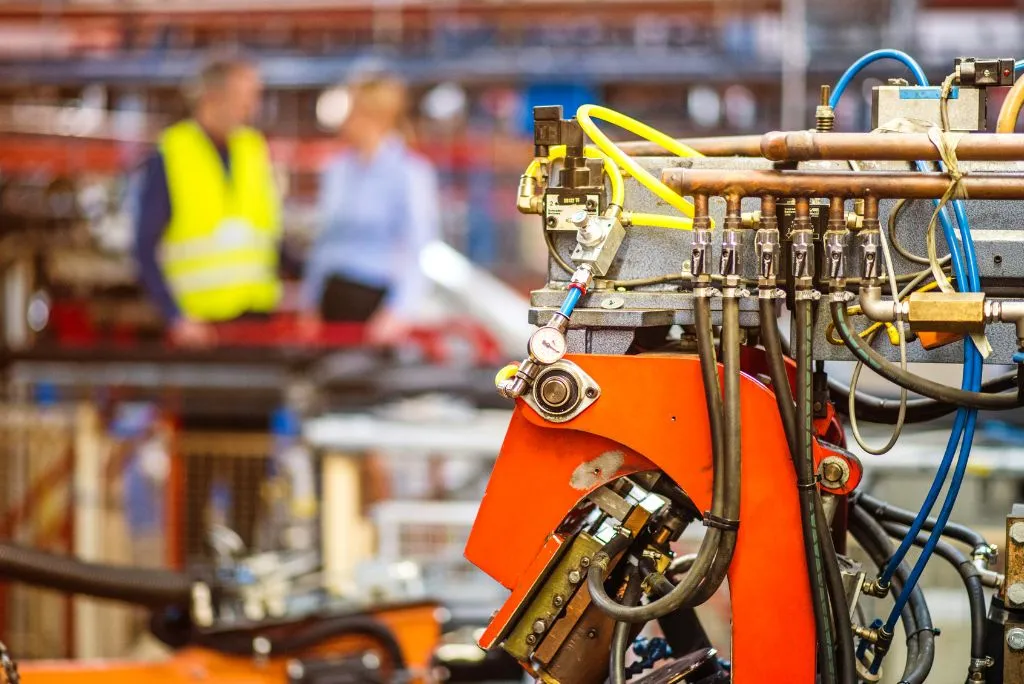
Hydraulics can be found at work as an effective means of generating mechanical energy. Hydraulic action, in its simplest form, is the use of compressed fluid to effect motion.
Lifts, construction machinery, shock absorbers, brakes, power steering, and even the steering systems of spacecraft all use hydraulics. Because of this system’s significant lifting, any hydraulic fluid leaks must be fixed as soon as possible!
Helpful Tips on Fixing Hydraulic Fluid Leaks
A leak’s location must then be determined. For this, remove the pressure from the system and examine the seals, connectors, and joints using protective gloves.
Fittings and couplings that leak can often be repaired by simply tightening them. It may be necessary to replace worn seals and hoses.
Tip 1: If you find a leak, fix it as quickly as possible.
An exterior leak is evident to the naked eye. Put it off no longer. A leak in your hydraulic system may foreshadow a more significant issue affecting performance and efficiency. Find a quick solution to the problem.
Tip 2: Always use protective gloves when dealing with hydraulic fluid.
Avoid using your bare hand to find leaks. Burns from 300°F or higher hydraulic fluid can occur in minutes. Pinhole leaks of high-velocity liquids can be devastating if they hit your hand. This injury requires immediate medical treatment, could cause amputation, and violates safety rules. Beware.
Tip 3: If there is a leak, no flames should be around it.
Always make sure to keep any kind of flame at least a safe distance from any sort of leak point. Unfortunately, clouds of combustible vapor can be produced by even the most minor pinhole leaks, which are commonly overlooked.
Tip 4: Turn down the pressure in the system.
Pressure must be removed before checking a hydraulic system. It retains even if liquids flow slowly. Depressurizing the system reduces the chance of hydraulic fluid bursting during the examination. After shutting down, trapped fluid and back pressure may remain. Even when the system is off, use caution.
Tip 5: Always make sure your lubrication is up to par.
Contaminated lubricants cause 80% of machinery and equipment breakdowns. Overheating causes oxidation, and dirt, water, and worn metals cause contamination and leaking. A dropped fitting before reassembly could pollute the hydraulic system.
Tip 6: You should clean your plugs and connectors
Before replacing a fitting, clean the ends. It keeps the hydraulic system clean. A conical washer can prevent leaking flare joints. Using pipe thread connectors with an elastomeric seal will assure water tightness.
Tip 7: Do change out O-rings and other fittings when necessary.
Even if you are reassembling a reusable fitting, you should always replace the O-rings. A damaged O-ring will no longer provide a reliable seal after being reassembled. Replacing a fitting is always more cost-effective than buying a brand new machine.
Tip 8: Always use the proper amount of torque when tightening.
If the torque applied to a flare joint is too low, the seat won’t make contact with the tube, and if it’s too high, the connector and tube could be damaged. Over or under-torquing a compression joint might cause the ferrule to “crush” too much or too little. From time to time, a fluid leak can be traced down to a simple cause: a nut that has come loose. To fix this, simply snug up the nut.
Tip 9: Do establish a routine for upkeep.
There is a correlation between hose and fitting inspections and the frequency of unexpected problems. Ensure there are no leaks, cracks, or blisters. Change the filters and wipe down the machines regularly. Keep an eye out for hydraulic dripping; if you see it, track out the source of the leak before it causes any severe damage or expense.
Effective Tracing of Hydraulic Fluid Leaks
- Frequent Inspections
Each machine must have its leaks checked as part of its regular maintenance. A visual check will do the trick nicely. Turn on the machine, get it up to operating pressure, and then check for fluid leaks or drips by visually inspecting all hoses and connecting points. Also, look for puddles or other unusual wet spots on the floor around the machine, as these could be signs of an exterior leak.
- Monitoring Fluid Levels
External leaks will result in lower system fluid levels; thus, monitoring these levels is a valuable method to stay informed of any changes. Having organized records will be helpful. Understanding how much fluid is being lost from the system during regular operation can be determined by keeping note of when and how much fluid has been replenished over time. Insight into this will aid in detecting deviations from the norm, which may signal the presence of a leak in the system and necessitate repair.
- Locating the Hydraulic Leak’s Origin
It may be difficult to pinpoint the leak’s source if fluid flows from other areas of the device. For instance, fluid may be pouring from the hose’s connection to the valve, but the hose itself may be split down the middle, with the fluid traveling down the length of the hose before dripping off at the connection.
Problems Cause by Hydraulic Fluid Leaks
Leaks from the outside can have far-reaching effects, including on profits, employee welfare, and environmental quality. Most notably, some of the issues are:
1. Expendable fluid
A significant issue is a fluid loss. Every time a drop is lost, it must be replaced at a cost.
2. Producing heat
Inadequate fluid levels in the system can lead to overheating, varnish buildup, and early hose and seal failure. Maintaining a consistent temperature for hydraulic oil contains additional details.
3. Pollution and other ecological dangers
Fluid leaks from mobile machinery can be especially problematic since they risk polluting the environment and are difficult to clean up. Small or discovered leaks will cause less ecological harm, but more significant leaks can have serious consequences. Slip and fall incidents, still a prominent source of injuries in the workplace, can be brought on by hydraulic oil that has pooled on the floor in industrial settings.
4. Toxic contamination of the system
External leaks form bridges between the outside world and the hydraulic fluid. If the crack is big enough, particles may be able to enter the space left behind by the fluid. Fluid contamination significantly contributes to hydraulic systems’ deterioration and eventual failure. It is essential when the machine is used in a mobile setting, where it is frequently exposed to dirt.