How to Remove Water From Hydraulic Oil
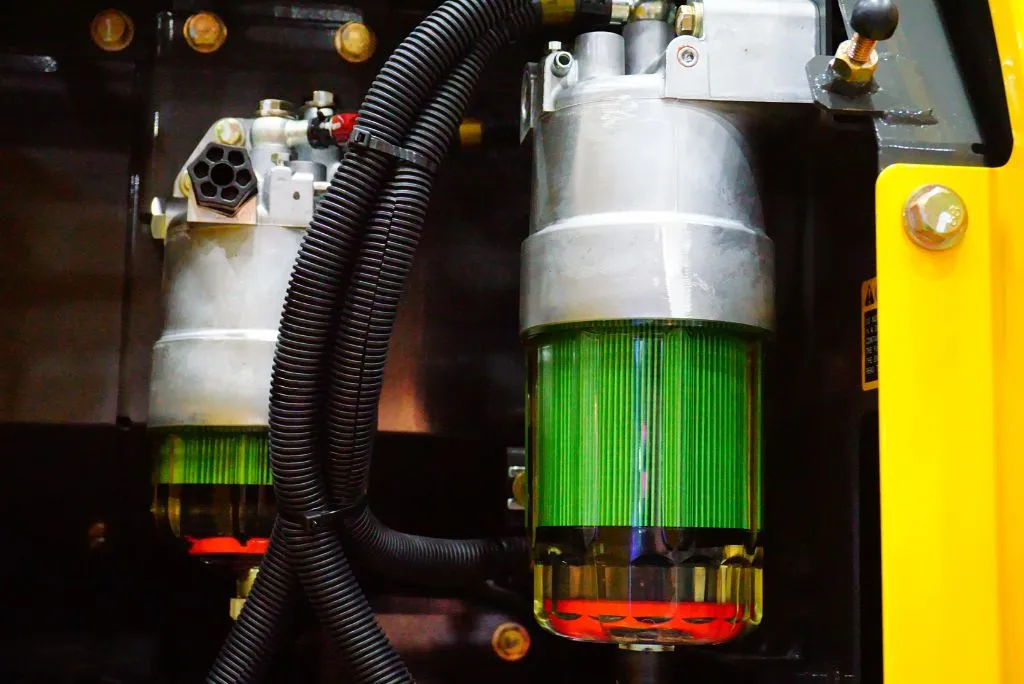
Hydraulic fluid is used to maintain the smooth operation of the hydraulic system.
Water and other contaminants can sometimes find their way into the system, diminishing its effectiveness. However, as part of regular upkeep, the hydraulic oil should be swapped out at predetermined intervals, such as after a certain number of hours of use.
Maintenance of the hydraulic system, including frequent fluid changes, is essential to ensuring its continued reliability and efficiency.
Water Contamination Symptoms
Hydraulic systems are susceptible to issues caused by moisture. It is anticipated that there will be some water in the fluid. However, the molecular chemistry of hydraulic oil starts to change when too much water is dissolved in the oil.
Cloudy oil is the most obvious indicator of water contamination.
Depending on the fluid, the oil may also have a muddy hue. The oil will have air bubbles, making it look like chocolate milk. However, this is the bare minimum of water that can cause oil cloudiness. As a result, a higher degree of water saturation is possible.
Fluid power reduction is another indicator of water contamination. Due to the presence of dissolved water, the fluid loses its viscosity and, therefore, its ability to transmit fluid power.
Various Methods in Removing Water from Hydraulic Oil
The demulsibility property of a fluid is its capacity to lose its water content. This characteristic may not be present in all fluids. However, this property and its impact on system performance should be considered before deciding on fluid for your application.
There are three different ways water can exist in hydraulic oil: as an emulsion, in solution, or as free water. Incorporating water into hydraulic oil compromises its chemical and mechanical integrity.
The physical properties are affected by an increase in viscosity and a decrease in load-carrying capacity. The chemical properties suffer from oxidation, reduced dielectric strength, and hydrolysis. Corrosion, wear, filter plugging, and cavitation is all issues that can arise in a hydraulic system due to the destruction of these chemical and physical properties.
Many techniques exist for efficiently separating hydraulic oil and water. Here are a few examples:
1. Separation by Gravity
Separation based on specific gravity is an old-school and environmentally friendly method. This method is less expensive and requires less in the way of heat or chemicals.
It is the method of choice with free water in the hydraulic fluid. The specific gravity of water is typically higher than that of oil. If the fluid is not moved for a while, it will sink to the bottom of the reservoir.
2. Centrifugal Segregation
It is an alternative technique for removing the water from the oil. When compared to gravity separation, centrifugal separation is far superior.
By spinning the fluid, the method will amplify the disparity between the specific gravity of the fluid and water. A little coagulant salt is added to the mixture before centrifugation to help things along.
3. Converging Isolation
When dealing with low-viscosity oils, coalescing separation is the most effective method for water removal. To coalesce means to become one.
With this device, water droplets of various sizes will be merged into larger ones that can be drained away more efficiently. Countless industries use this technique, from the oil and gas industry to the petrochemical and refined chemical industries to the parts cleaning facility.
4. Separation of Absorbent Polymers
This technique can eliminate a minimal quantity of free and emulsified water. A polymer filtration system removes the oil from the water. The filter’s retention of water causes polymer expansion. In other words, this setup is not made for uses that involve a lot of liquid.
5. Substitution of Vacuum for Ordinary Pressure
This technique can remove free, emulsified, and dissolved water. Vapors are subjected to various temperatures before vaporizing, condensing, and cooling. It can eliminate water and contaminants like solvents, fuels, and refrigerants.
6. Dehumidification of the headspace
It is an additional strategy for removing aqueous phases in various states like free, emulsified, and dissolved. Extracting air from a sump’s headspace is the necessary action.